HRL Labs
During my second co-op at HRL, I worked on projects for Boeing and General Motors. I was responsible for designing and analyzing a multi-part assembly made of metal with a composite skin. I also layed up composites and performed material tests in Instron machines to validate FEA assumptions.
In addition to the structure, I performed numerous electromagnetic simulations to match experimental results and validate existing models.
​
Tools Used: SolidWorks, SolidWorks FEA, COMSOL, Instron Machines, Composites
​
Note: All images are sourced online and are only to provide visual aid to descriptions.
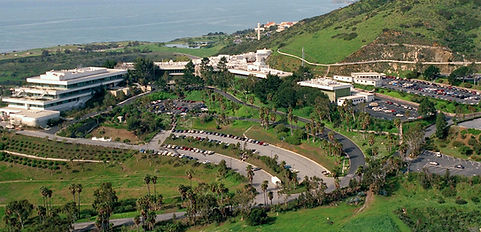
Structure Design
The Problem
-
A structure needed to be designed for aerial operation that was cheaper than the existing solution
-
The structure is subject to high multi-axial loading, but is only single use
-
Material properties needed to be confirmed for composite being used in the structure
​
Solution
-
Designed and iterated on a 20-foot-long glass fiber composite reinforced metal structure in SolidWorks with over two dozen components
-
Performed FEA in SolidWorks and optimized the structure for the lowest cost using easily manufacturable components
-
Created composite samples and tested properties in Instron machines to validate FEA assumptions
Result
-
A master model drivel assembly was created for ease of future revision
-
Drawings were created for each of the parts for future orders
-
Parts were ordered for initial prototyping of design

Example of SolidWorks FEA
Electromagnetic Simulations
The Problem
-
During high power operation, magnets in electromagnetic systems can demagnetize which limits their temperature and power operating range
-
Experiments have been run testing different magnet configurations, but they are lengthy and there isn’t enough time to try out every configuration
Solution
-
B-H curves from experimental data were imported into COMSOL and a magnetic environment was created
-
A reverse field was applied to the magnet model to test the resistance to demagnetization
-
Models were created to test different arrangements as well as different materials
Result
-
Using results from one set of tests, a model was able to be created that could be used to characterize demagnetization in multiple new configurations saving time in running experiments
-
Different configurations were proven to show varying resistance to demagnetization that could be used to improve performance

Example of COMSOL EM Simulation